September 21, 2020
Operational Efficiency during COVID
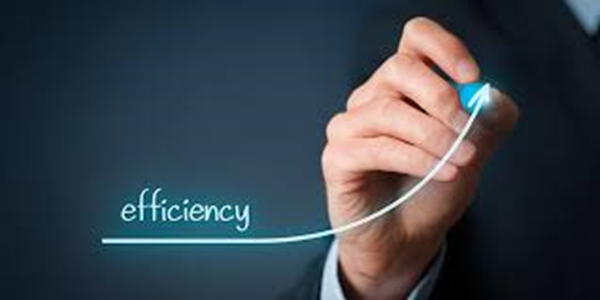
Realistic objectives are the catalyst for a culture of operational efficiency. The COVID-19 crisis has increased production costs for many businesses while customers are increasing their requirements. In this context, it’s more important than ever to deliver a quality product at a good price.
Starting Point: Identify your customers’ needs
Any operational efficiency process necessarily begins with identifying customer needs. This involves a rigorous analysis of the anticipated order volumes and types of products or services sought.
Another consideration is ‘takt’ time, a German term that refers to the production rate required to meet customer demand. This analysis will help you adjust your operations to produce what you need at the right time and efficiently. For example, it will give you the opportunity to determine the size of workforce you will need. Having too few employees could stop you from meeting demand while having too many would be inefficient. In a context where customer needs fluctuate rapidly, it’s important to carry out this sales and operations planning exercise on a regular basis to ensure that your production is closely aligned with demand.
3 key operational efficiency practices
Once your production plan is firmly in place, you’ll be able to go a step further by introducing these three key operational efficiency practices.
1. Establish the right performance indicators
To meet your production goals, you’ll need performance objectives that are ambitious but realistic. Businesses in all sectors can benefit from setting objectives, whether they be manufacturing businesses, distribution centres or service sector businesses. If you achieve the objectives, it’s because you’ve done well, and the new approach needs to be standardized. If the objective isn’t met, you need to find out why and establish a strategy with the team to achieve it. What you want to avoid is an objective that is never going to be met. While an objective that is met every day is too easy. A middle ground is needed.
The most common performance indicators
Quality: Quality is often measured by looking at the percentage of rejects. This indicator is often combined with an indicator from the customer, whether it be the percentage of returns or the number of customer complaints.
Efficiency: Efficiency or production cost is an important measure for businesses. This indicator is often measured by comparing the time budget for performing an identified task with the actual time spent on that task.
Delivery time: Often considered the most important indicator, delivery time measures the time taken from receiving the order to final delivery, the idea being to significantly reduce production time, waste and mistakes, as well as to increase customer satisfaction. This measure usually has a ripple effect on the other indicators.
Health and safety: This indicator has become non-negotiable during COVID. While businesses are used to keeping track of the number of days without accidents or the number of days without minor incidents, it is now a matter of ensuring that no employees are affected by the pandemic.
2. Organize daily team meetings
The second practice to be implemented is a daily team meeting for supervisors. This 10—15 minutes meeting will bring your team together to follow up on your production plan, review the dashboards and identify the actions to be taken as well as the people responsible. It will also allow you to review the previous day in order to look at successes and identify areas for improvement. In a crisis situation, these meetings can be held twice a day, at the beginning of the shift and at lunchtime, to help teams adapt quickly to changing customer demands.
3. Introduce digital technologies
Businesses that want to remain competitive today must consider digital 4.0 technologies. These technologies include, for example, manufacturing digital dashboards, which provide a real time visual representation of performance indicators. This data will help you alert key personnel to situations that require immediate attention or detect and analyze the root causes of unplanned downtime and rejects. Daily management systems are another type of software that is indispensable for manufacturing businesses. They enable managers to monitor the progress of a project, task or process on a daily basis. They can also assist in automating workflows, task assignments and reminders, while ensuring that roles and responsibilities are clear.
Encourage team participation
Employee participation is key for implementing these three continuous improvement practices. To encourage employee participation, one technique is to measure the number of process improvements introduced by the team. It’s also important to train employees to understand the basics of operational efficiency, such as waste and added value. Now more than ever, we need employees to participate, we need their ideas to improve.